How to Create Material Master in SAP MM
The Material Master in SAP is pivotal for defining the characteristics of a new material to regulate its behavior across various transactions. There are two primary methods for creating every material:
- Utilizing transaction MM01, commonly preferred in a productive environment.
- Mass creation, typically employed once during the transition of materials from a prior system to SAP ERP.
Our current focus is on transaction MM01. The topic of mass creation, an advanced tool, will be addressed later, once there is sufficient understanding of the material master views and organizational levels.
How to Create Material Master in SAP MM
Creating a Material Master in SAP MM involves a detailed, step-by-step process. This procedure is critical for ensuring that materials are correctly cataloged and managed within the SAP system. Here’s an expanded guide on how to create a Material Master in SAP MM:
Step 1: Industry Sector and Material Type The process begins with transaction MM01, which is the gateway to creating a material master record. Upon executing MM01, you’re directed to an initial screen requiring basic material information.
- Industry Sector: This field is crucial as it categorizes the material according to the industry segment. A common sector is ‘M’ for Mechanical Engineering, but this varies depending on the specific industry context of the material.
- Material Type: Here, you need to specify the type of material being created. Options include FERT (Finished Products), ROH (Raw Materials), HALB (Semi-Finished Products), and HAWA (Trading Goods), among others. The choice of material type influences how the material will be processed and managed in the system.
Step 2: Basic Data After the initial categorization, you enter the Basic Data screen, where you provide detailed information about the material, such as its description, unit of measure, and weight. This data is essential for accurately identifying and tracking the material across various SAP modules.
Step 3: Classification In this step, you classify the material to further define its attributes. This classification helps in sorting and locating materials within the system, facilitating better inventory control and reporting.
Step 4: Sales Data If the material is a sales item, this step involves entering sales-related information, like sales unit, pricing, and tax classification. This data is vital for sales and distribution processes.
Step 5: Purchasing Data Here, you enter details relevant to the purchasing of the material, such as the purchasing group, order unit, and vendor details. This information is crucial for procurement processes.
Step 6: Accounting and Controlling Information This involves inputting financial data related to the material, including valuation class, price control, and costing data. This information is necessary for accurate financial accounting and controlling.
Step 7: Review and Save Finally, review all the entered data for accuracy and completeness. Once confirmed, save the material master record. This final step solidifies the material’s presence in the SAP system, making it available for transactions and processes.
This comprehensive approach ensures that each material is accurately represented in the SAP MM system, facilitating effective and efficient material management.
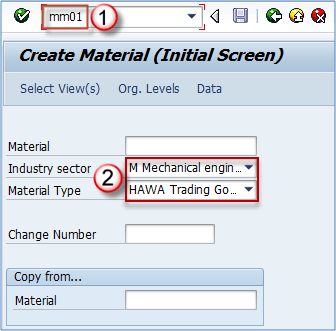
Step 2: Selecting Master Data Views for Material Creation in SAP
In SAP, when creating a Material Master, Step 2 involves a critical decision-making process where you select specific views of the master data to create. This step is accessed by clicking on ‘Select View(s)’, which allows you to tailor the material master record according to your requirements.
- Selecting Views: Here, you have the flexibility to choose which aspects of the material master you want to establish. This could include ‘Basic Data 1’, which covers fundamental material information, and ‘Sales Org Data 1’, essential for sales-related specifications.
- Extension of Material Master Data: An important aspect to remember is the ability to extend the material master data at a later stage. If initially, not all necessary views are selected, they can be added subsequently. This feature offers flexibility and ensures that the material master can evolve with changing business needs.
- Using the Check Mark: In the selection process, you will find an option button, usually marked in blue, to select all views. This option, while available, is seldom used in a productive environment due to its broad scope. More often, specific views are chosen to maintain a focused and relevant material master record.
This process of selecting views is vital as it determines how the material will be represented and managed in various modules of SAP. By making informed choices at this stage, you ensure that the material master is aligned with both current and future business requirements, enhancing efficiency and accuracy in material management.
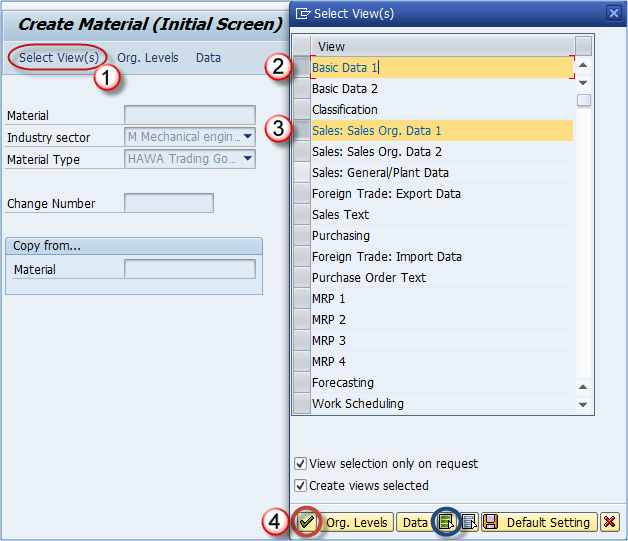
Step 3: Entering Organizational Levels in Material Master Creation
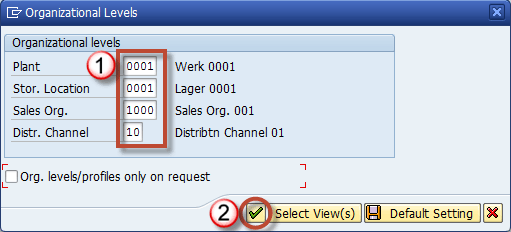
Table of Material Master Views and Their Organizational Level Connections
Here is a comprehensive list of the organizational levels required for establishing material master views.
Material Master View | Organizational Levels |
---|---|
Basic data (1 & 2) | None |
Classification | None |
Sales organization data (1 & 2) | Plant, Sales Organization, Distribution Channel |
Sales General | Plant |
Foreign Trade – Export data | Plant |
Purchasing | Plant |
MRP Views | Plant, Storage Location, MRP Profile |
Forecasting | Plant, Forecasting Profile |
Work Scheduling | Plant |
General Plant Data (Storage 1 & 2) | Plant, Storage Location |
Warehouse Management 1 | Plant, Warehouse Number |
Warehouse Management 2 | Plant, Warehouse Number, Storage Type |
Quality Management | Plant |
Accounting (1 & 2) | Plant |
Costing (1 & 2) | Plant |
GETTING STARTED
Transform Your Business Today - Get Your Custom Quote Now
- Tailored Solutions: Receive a personalized quote that aligns perfectly with your business needs and goals.
- Expert Guidance: Leverage Orlando Monteiro's extensive experience in business transformation and digital innovation.
- Cost-Effective Strategies: Discover how you can optimize your operations and reduce costs with our expert solutions.
- Immediate Impact: Start seeing tangible results in your business efficiency and productivity right away.
- Long-Term Success: Embark on a journey towards sustainable growth and competitive advantage with our strategic guidance.
Leave a Reply